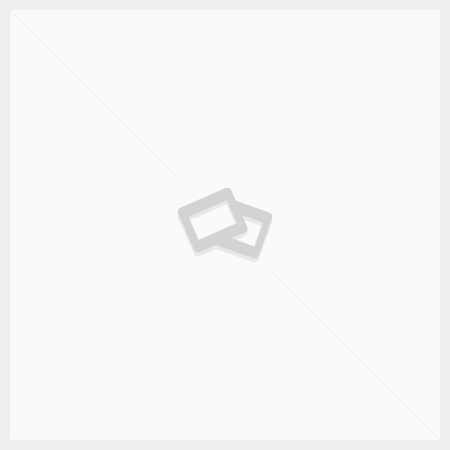
When our team works with mid-market companies heading into an ERP selection project, we’re often asked to share insight into the ERP systems that best serve those organizations operating multiple facilities across multiple regions.
In the ERP world we refer to a group of requirements as the “multi’s.”
The Different Types of “Multi’s”
- Multi-Company enterprises which are organizations that operate with multiple tax ID’s. Many ERP systems can track operations at this level, but some systems require a separate instance along with multiple databases.
- Multi-Language enterprises which need the ability to display a screen in a different language based on the user ID. Many systems offer this functionality, but the number of languages supported could be an issue.
- Multi-Currency enterprises which need the ability for the ERP system to track transactions in a range of global currencies, while the base accounting system calculates financials in US dollars. Most ERP systems offer this feature. Note that inventory valuation in different currencies can be an issue.
- Multi-Plant is a designation that is similar to multiple companies. Here, the organization operates out of multiple manufacturing locations, but does not need multiple tax identification.
Key Business Issues
When it comes to ERP implementation, the biggest issue facing the Multi-Facility enterprise is the ability to setup the accounting system and the planning system to simultaneously handle multi facility / plant transactions in real-time.
The issue is that both accounting and planning/manufacturing use the plant ID, or branch ID, or site ID. Note that depending on the ERP vendor, these terms will vary. The accounting system is setup to understand plant/site level profitability. The planning system wants to break down the walls and plan across multiple locations to best utilize capacity. Therefore, a conflict arises.
Furthermore, if the enterprise has a need to setup multiple companies so that there is a different tax ID for each plant, this greatly complicates the ability for an ERP system to make product across companies. The system will require a customer order and purchase order, and will restrict interplant routings. If a company merely wants to treat each plant like a separate company then the issue is mitigated. But as soon as the capacity of multiple plants needs to be co-mingled to meet the needs of customers, there will be system limitations for many ERP packages.
The multiple company and multiple plant environments have emerged as a significant issue facing manufacturing organizations embarking upon an ERP comparison. This factor may drive our clients to look at larger, more complex, tier one ERP vendors.